Raku Pottery Workshop
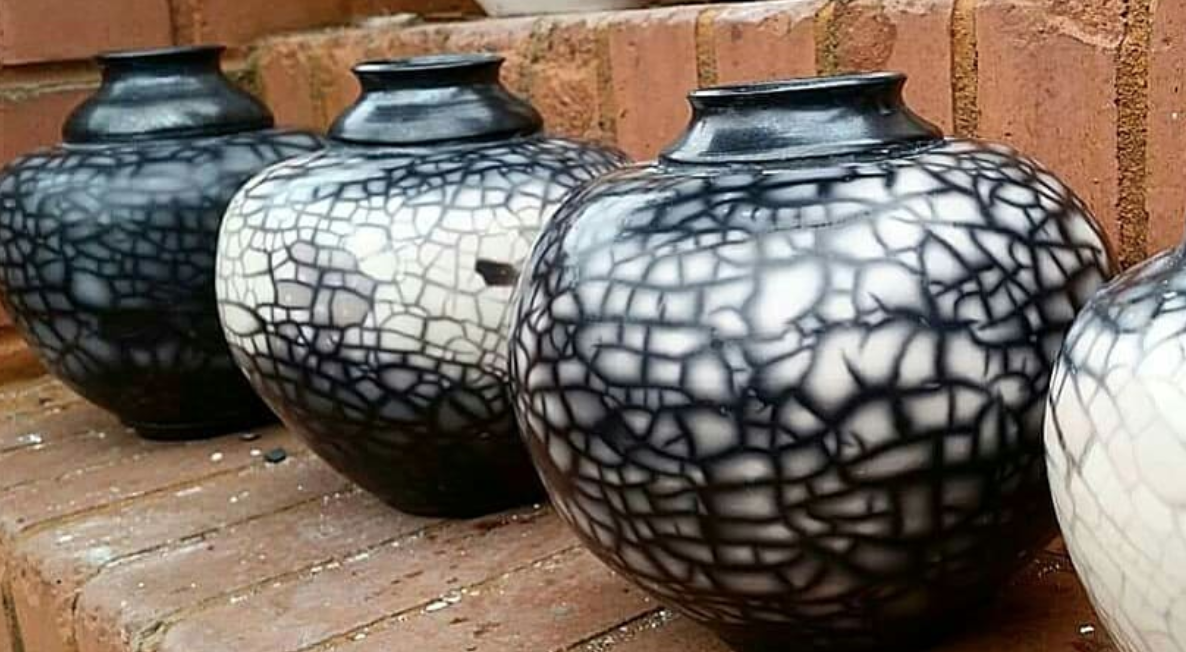
Raku Firing!
Saturday Aug 25th 10am - 6pm
Sunday Aug 26th 12pm - 5pm (for over flow)
All levels of clay experience are welcomed.
There are 2 types of raku workshops to choose from.
Option 1:
You will be able to select 6 bisque ceramic pieces made by myself to glaze and fire. Each piece is yours to keep. The pieces will be of various sizes. This requires no ceramic experience at all. ($185)
Option 2:
Bring your own pieces, up to 6, to be fired. They must be no taller than 10in and no wider than 6 inches. Because of spacing, plates and wide bowls should be avoided for this firing. Your pieces must be bisque fired to either cone 06 or 04. Glazes will be provided. ($85) Feel free to email if you have any question about your pieces.
In the morning you will receive instruction on how to glaze and prep for 3 different types of Raku firing .
1) Western Raku Firing -
Fired to 1850F and involves glazes, sawdust and other combustable materials. The glazes will craze when we pull them from the kiln. This happenes as they adjust to the extreme temperature drop and the smoke from the reduction chambers will create black lines in the crazing.
2) Naked Raku Firing -
Fired to 1450F the pots are coated with terra sigillata to create a smooth background. This firing involves no glaze but a thick slip applied right before the piece is placed in the kiln. The slip will start to dry, crack, and slightly separate from the pot. Once it is pulled from the kiln and placed in its reduction chamber the smoke will penetrate the open cracks and leave striking lines similar to cracked desert ground.
3 ) Horse Hair Raku -
Fired to 1400F, the pots are coated with terra sigillata to create a smooth background. This firing also involves no glaze. Each piece, once it has been pulled from the kiln, will get horse hair or bird feathers placed on it. As the hair or feathers burn they will leave a shadow behind, creating beautiful smokey images.
Each firing has it own beauty and you will get to chose which firing and glaze is right for each piece.
As the kilns are firing we will prep the sawdust, combustible materials and reduction chamber pots for each piece, and repeat after each kiln is unloaded. After all the pieces are pulled from the kiln they will sit in reduction for 20 mins. It is here that the magic happens, and the red hot pots cool and allow the smoke to alter their appearance. After, they will be placed in water to be scrubbed cleaned.
In this workshop we will take each piece from start to finish in under 2 hrs.
Talk about instant gratification!!
The second day of the workshop is for over flow. If all the pots do not get fired on Saturday, we will resume firing the next day, Sunday, from 12pm - 5pm.
Glaze Colors:
- Clear Crackle
- Orange Crackle
- Cobalt Blue Crackle
- Turquoise/ Green
- Yellow Crackle
- Dark Rose Crackle
- Matte Copper (ranges from purple, blue, gold to green where the reduction happens)
- Copper (ranges from shinny penny color to metallic black )
Safety!
Since we are working around very high temps, cotton clothing, long sleeves, jeans and closed toe shoes are a must.
After the first “pull” I will demonstrate, on a cooling kiln to any student who is willing to pull pieces from the kiln with me. Any student who wishes to do so must wear a face heat shield and gloves to the elbow which will be provided.
Make sure to bring water!
Tools!
All tools will be provided. If you have welding gloves and would like to bring them, feel free. Make sure to wear clothes you don’t mind getting dirty or smelling like a camp fire.
Lunch!
We will break for lunch around 1. The exact time for lunch will be dependent on how fast the kilns fire. Bring your own lunch.
Instructors
Delores J Farmer
Contact us
- Class Coordinator
- cl••••s@lib••••c.org
Location
Classifications
Categories
- Ceramics classes
Age Groups
- All